Center for Microfibrous Materials Manufacturing creates meaningful impact through innovation
Published: Oct 27, 2023 3:40 PM
By Joe McAdory
Thousands of jet-powered commercial airplanes soaring across the continental U.S. and western Europe skies are protected from lighting strikes by use of patented conductive additives to eliminate static charging — technology originated at Auburn University's Center for Microfibrous Materials Manufacturing.
Beyond the earth’s atmosphere, dozens of weather satellites employ batteries powered by nickel fiber electrodes developed by technology that originated from the Center for Microfibrous Materials Manufacturing.
See those electric vehicles that silently populate our roads? Go-juice is generated from batteries utilizing high-rate liquid double layer capacitor electrodes for pulse power applications, also developed by technology that originated from the Center for Microfibrous Materials Manufacturing.
Even state-of-the-art gas masks worn by NATO and U.S. soldiers were developed … well … you get the picture.
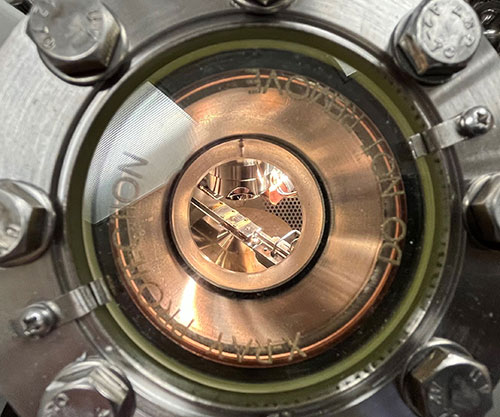
“We have so many success stories,” said Bruce Tatarchuk, the Charles Gavin III Professor of Chemical Engineering, director of the Center for Microfibrous Materials Manufacturing. “Here’s another one… we just sold a commercial reactor that takes agricultural waste and turns it into renewable jet fuel. Because of bio waste from landfills, poultry farms, cattle farms, pig farms, etc., we have even more patented technology where we can take the sulfur out of these biodigester gases and produce clean sulfur as an animal feed supplement, as opposed to having to landfill it, or flare it and send it into the environment.
“Our legacy isn’t just writing journal papers and counting citations. We innovate and create technology to the point where there's a patented product. Innovation is where real impact is.”
Founded in 1996, the Center for Microfibrous Materials Manufacturing was created to facilitate research development, education, technology transfer and economic development by establishing a small-scale manufacturing facility to produce/invent microfibrous materials.
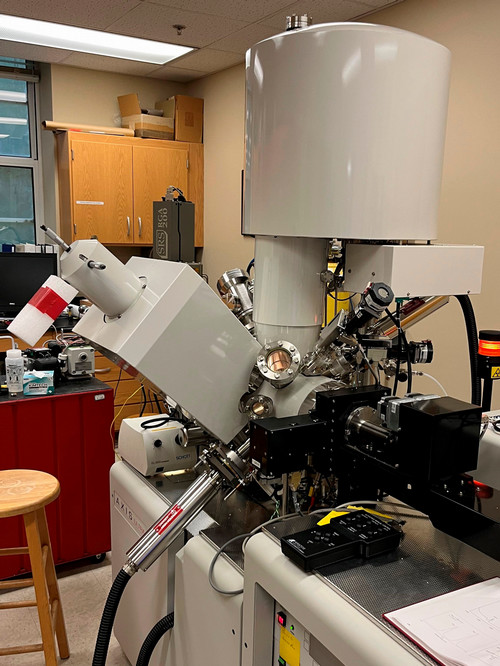
Whereas the center’s research is conducted on campus at Wilmore Engineering Laboratory and Ross Hall by Department of Chemical Engineering faculty, staff and graduate students, much of the commercial design and product development takes place off campus, where the baton is passed to IntraMicron – a leading technology manufacturing and development startup founded by Tatarchuk and others in 2001 and located at the City of Auburn Technology Park West.
IntraMicron is one of five global producers of micron diameter metal fibers and houses several process-integrated wet-lay machines for web layup, sintering, cutting and forming operations, reactor/electrode loading stations, analytical quality assurance/quality control equipment, and other related manufacturing and packaging equipment.
Tatarchuk was formally recognized in 2014 with his induction as a Fellow into the National Academy of Inventors for “inventions that have positively impacted mankind.” It’s no wonder Auburn and IntraMicron Techology’s portfolio stands at more than 100 U.S. and foreign patents.
“Our efforts will be extensively leveraged not only through existing contracts and grants, but also through new and larger contracts emphasizing industry-university cooperative efforts focused on development and commercialization,” Tatarchuk said. “Such efforts are timely and provide good matches to current national trends emphasizing industrial downsizing/outsourcing, increased national competitiveness, and better leveraging of national resources, including universities.”
Tatarchuk is not only a master innovator, but a master at turning innovation into intellectual property.
“We are redefining technology transfer not as a discontinuous, ‘hands-off and hope’, but rather as a supportive and continuous ‘hands-on’ partnership with industry,” he said. “By providing a platform for both scale-up and development, we enhance the training, experience, entrepreneurship, and overall value of the student while at the same time offering a timely attractive and cost-effective service to industry.
“The opportunity to take our technologies and spin them off into the Technology Park and do this locally, right here in Auburn — that's when we become the Research Triangle. That's when we become Silicon Valley.”

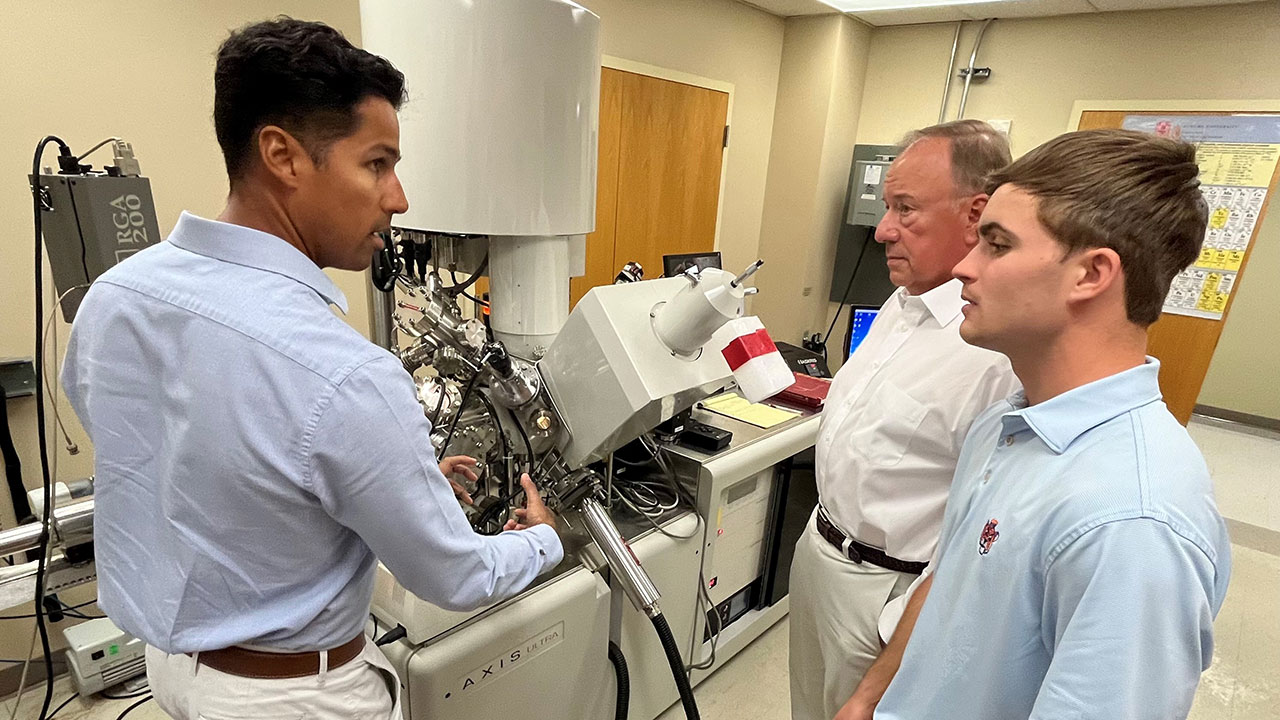
Chemical engineering graduate students Felix Mendoza, left, and Jacob Faulkner discuss upcoming research strategies with Center for Microfibrous Materials Manufacturing Director Bruce Tatarchuk.