AU lean manufacturing lab builds future generation of engineers
Published: Oct 14, 2020 4:05 PM
By Virginia Speirs
When you think of a college-level industrial and systems engineering lab, your first thought is likely nowhere close to a toy car assembly line, but that is exactly what this Auburn University lab is. Commonly referred to as the “Lego Lab,” students studying industrial engineering use this lab to, quite literally, build their engineering skills through the understanding of an industrial production line.
By working in a team environment and implementing lean manufacturing principles to achieve the stated objectives, students develop the equivalent of 10 years of manufacturing experience by the end of the semester, according to Tom Devall, auto manufacturing initiatives director and professor of industrial and systems engineering.
“The purpose of the lab is to provide a ‘hands on’ learning experience for our undergraduate students,” Devall said. “The primary topic we teach within the lab is the Toyota Production System (TPS) or lean manufacturing. We also teach fundamental Programmable Logic Controller (PLC) and robotics.”
The philosophy of the lab is to create a complete manufacturing system that produces a Lego vehicle at a typical automotive manufacturing pace, which is one unit per minute, Devall explained. It usually takes lots of practice for the students to achieve this, but by the end of the lab they are well adjusted to the process, methods and pace of a typical auto manufacturing assembly.
“Most of the time, students go into the lab very confidently,” Devall said. “But the fact is, the probability of error is multiplied by the 15 stations of the assembly line, and that means by the time the car gets to the end of the line, it’s a basket case in a lot of ways. So, throughout the semester, their job is to figure out why they are failing and what can they do to fix it.” The concepts of lean manufacturing learned in class lectures are applied to the problems the students experience.
Although a real auto manufacturing assembly plant has a more complex product with many more parts and steps, the concept is still the same in this lab, Devall explained. Students build two variations of a toy car, each with about 250 parts, and their goal is to build 45 error-free models in 45 minutes. Through this, students learn how to work together to build a flawless product with efficiency and strategy, using various procedures and methods.
“The way to think of this is it’s just like a regular factory because we are producing a product that has a multi-part complexity,” Devall said. “[The students] have to produce it at the rate of an assembly plant, and an assembly plant builds a car every minute.”
This lab was recently awarded a $65,000 grant by the DENSO North America Foundation, the philanthropic division of leading mobility supplier DENSO. The grant helped Auburn acquire materials needed for the lab’s future success, including an error-proofing and light-guide system. Despite the complications caused by COVID-19, the materials have arrived on-time and according to schedule.
“I think everything is on track so far,” Devall said. “We’ve got three pieces of the equipment and we have two more that we’re waiting for, so everything should be good.”
The lab shows much promise and is a popular attraction for events on campus, such as E-Day. Even representatives from large auto companies such as Honda have shown interest in the lab, Devall said, because of the simplicity of the concept yet the skill that it requires of the students.
“I like to think of it like taking a class on building a house,” Devall said. “You could read the textbook all the way through, know the information and pass the exam with an A, but there’s no way you could then go to a field and build a house, because no matter how much you study something like this, you can’t actually do it unless you practice it.”
One student in particular has been recognized for his outstanding performance in the “Lego Lab.” Nick Simmons, a graduate student in industrial and systems engineering, was named the 2020 J T. Black Lean Engineering Student of the Year for his “demonstration of a deep desire to learn, respect for people and commitment to continuous improvement,” Devall said.
“This lab has been one of the most beneficial learning experiences of my time at Auburn,” Simmons said. “It is a first-class educational tool that helped me experience real life manufacturing scenarios. With the help of the lab, I was able to better understand principles and techniques taught during lectures, and I was pushed to grow as a leader, student and coworker in the process.”
Simmons said he is extremely honored to receive the award and, although he never had the opportunity to meet Black, he is reminded through this award to continue to strive for excellence, leadership, respect and improvement, just as Black did. Black, who died in 2019, was a professor emeritus of industrial and systems engineering at Auburn whose specialty areas included materials processing and manufacturing systems design and engineering.
“I am thankful for the lab’s educational benefits, but I am even more thankful for the memories it brought,” Simmons said. “I bonded with my peers as we experienced the stress of a ‘manufacturing’ work environment. We solved problems together and worked to reach the goals set by our professor. The lab brought us a lot of laughter and personal growth along with a deepened desire to continue learning lean manufacturing.”
Media Contact: , cmontgomery@auburn.edu, 334.844.3668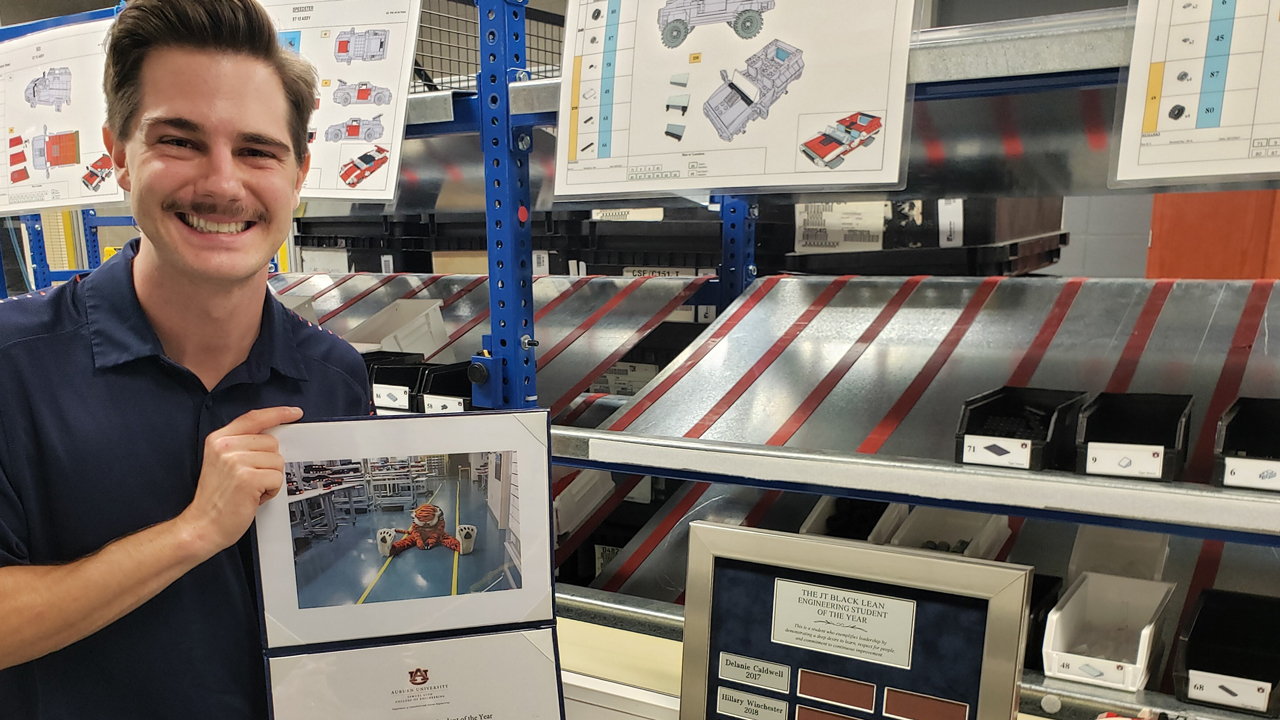
Nick Simmons, graduate student in industrial and systems engineering