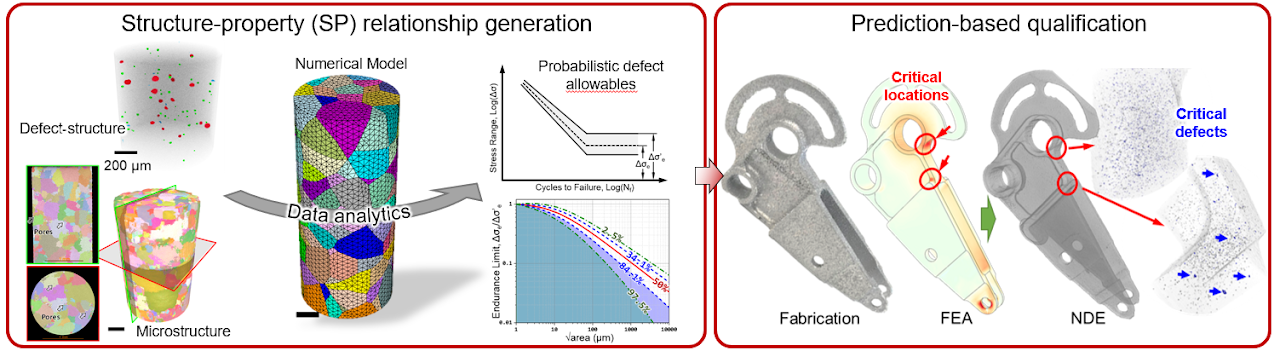
NCAME’s approach to additive manufacturing qualification for fatigue critical application is model-centric. The conventional generation of structure-property relationship is data intensive, can greatly benefit from numerical simulations. The current NCAME efforts centers on understanding the synergistic effects of defects and microstructure on the fatigue behavior of AM parts. With the knowledge, parts can be qualified at certain reliability and confidence for expected loads based on probability of failure. NCAME model-centric AM qualification at a glance:
- Non-destructive and destructive extraction of defect content and microstructure in AM parts
- Experimental fatigue data generation
- Calibration of numerical models for fatigue property predictions: including finite element-based models and crystal plasticity models
- Establishing probabilistic structure-property correlations
- Part qualification at given reliability and confidence for expected loads based on stress analysis, SP relationship, NDE
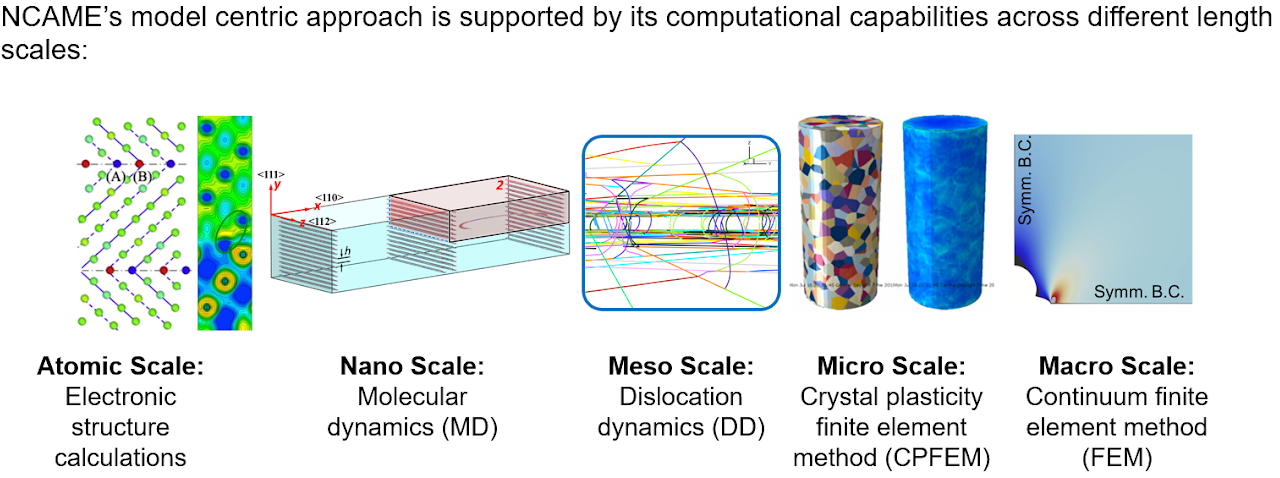
- Atomic scale: the segregation of impurity elements may weaken the grain boundaries in AM materials, which can be studied by electronic structure calculations, such as density functional theory (DFT).
- Nano scale: the operation of persistent slip bands (PSB), which are responsible for materials ’ fatigue damage, can be influenced by the compositional/phase heterogeneities specific to AM materials (such as the dendritic structures). This effect can be investigated using molecular dynamics (MD) on isolated dislocations.
- Meso scale: with the dislocation mobilities characterized by MD simulation, the operation of PSBs and the collective motion of many dislocations can be simulated using dislocation dynamics (DD).
- Micro scale: the deformation of an aggregate of grains (such as the fine columnar grains unique to AM materials) can be modeled using crystal plasticity finite element method (CPFEM) simulations.
- Macro scale: the finite element method (FEM) simulations can capture the overall deformation of AM parts addressing the effects of surface roughness and complex geometry. It can also investigate the critical role of volumetric defects in AM materials (such as porosity and lack-of-fusion defects) in the initiation of fatigue cracks.