NASA invests $1.5 million toward creation of Auburn University Space Manufacturing Initiative
Published: Dec 3, 2024 7:30 AM
By Joe McAdory
In-Space Manufacturing capabilities for structural and functional parts — tools, electronics, and sensors — is an inevitable part of future space activity. That’s why the world leader in space exploration is calling upon Auburn University.
NASA recently invested $1.5 million toward the Auburn University Space Manufacturing Initiative, led by Masoud Mahjouri-Samani, associate professor of electrical and computer engineering and Brock Birdsong, director of research at the Auburn University Applied Research Institute. This new initiative will focus on a circular manufacturing ecosystem where local resources can be reused for manufacturing new parts and systems on demand.
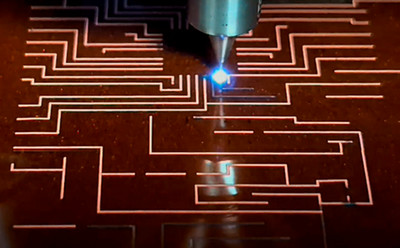
“The Auburn University Space Manufacturing Initiative is a prime example of Auburn’s leadership as a space-grant institution,” said Steve Taylor, senior vice president for research and economic development. “The Initiative’s research will be a driving force behind innovations necessary to advance critical missions and activities in space.”
“We must maintain our leadership in space, push the envelope of space exploration, and unleash its potential for both space and terrestrial applications,” said Mahjouri-Samani. “To do this, we must have the capabilities to manufacture parts and systems in space.”
The need for in-space manufacturing impacts multiple missions, Mahjouri-Samani said, including in orbit, on a surface (moon/Mars) and in deep space.
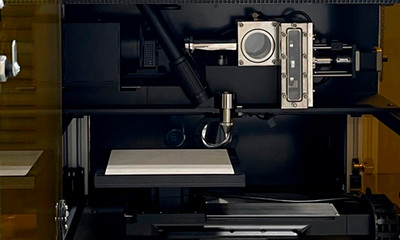
“The scarcity of resources in space, the microgravity environment and the high cost of transporting materials create challenges,” said Mahjouri-Samani, director of the university’s LASE-END lab who is building off of current research to create the space manufacturing initiative. “Scarcity of resources in space limits the use of current manufacturing technologies. Properly disposing of the out-of-mission and scrap parts in space is also a huge issue. These challenges demand manufacturing technologies that operate in space environments and, most importantly, can reuse and recycle the available resources.”
Mahjouri-Samani suggested the use of space junk.
“They’re already a big problem up in the space and are growing exponentially,” he said. “Why not convert them into necessary parts?”
Additive manufacturing (AM) technologies, Mahjouri-Samani said, are potential manufacturing candidates for in-space manufacturing needs, as they have made a paradigm shift in the design and manufacturing of complex parts and 3D structures. However, these technologies require well-defined sources of materials such as powders, sheets, and filaments for the printing process. For instance, the most common AM machines for 3D printing metallic parts, such as laser-based powder bed fusion or powder-fed directed energy deposition systems, require metal powders.
“These metal powders must be prepared in powder manufacturing facilities, properly stored and safely transported to the machine users for printing parts,” Mahjouri-Samani said. “These expensive technologies are less practical for remote locations, and they have complex safety requirements.”
Enter the Auburn University Space Manufacturing Initiative, which will use the funding to employ and develop new AM technologies that print parts and devices utilizing local resources. These resources will be used as feedstock for the on-demand and in-situ generation of micro and nano-powders for the printing process.
“In contrast to the current AM technologies where pre-existing powders are required, in our approach, particles will be generated on-demand using a laser ablation process of the solid parts,” Mahjouri-Samani said. “This unique approach allows us to address the space environment's scarcity and low gravity challenges for 2D, 2.5D, and 3D printing of functional and structural parts using local resources.”
Birdsong said by leveraging the university’s relationship with NASA and its world-class innovation in laser-based additive micro and nanomanufacturing technologies, Auburn is in a strong position to advance in-space manufacturing efforts.
“Our expertise in advanced manufacturing, and particularly NASA-funded on-orbit-printing functional structures and devices will allow Auburn to make important advances for in-space manufacturing challenge,” he said. “In addition, Auburn has demonstrated the in-situ generation and real-time sintering of ultra-small nanoparticles for in-space manufacturing of electronics and sensors, which is an ongoing research project with NASA.”
Media Contact: , jem0040@auburn.edu, 334.844.3447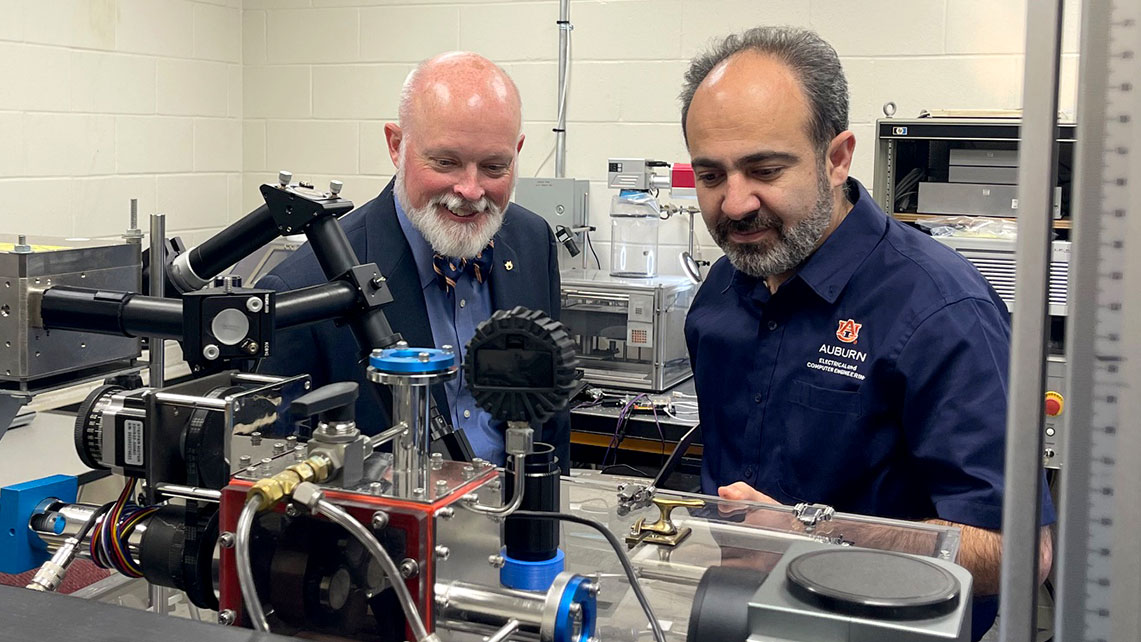
Brock Birdsong, left, director of research at the Auburn University Applied Research Institute, and Masoud Mahjouri-Samani, associate professor of electrical and computer engineering.