Auburn to expand Industry 4.0 research, education, training and innovation capabilities with $7.2M DoD award
Published: Sep 13, 2021 9:32 AM
By Cassie Montgomery
The Interdisciplinary Center for Advanced Manufacturing Systems (ICAMS) at Auburn University is the recipient of a $7.2 million award from the Department of Defense’s (DoD) Office of Industrial Policy’s Industrial Base Analysis and Sustainment (IBAS) Program to encourage small and medium-sized manufacturers to adopt the advanced technologies associated with Industry 4.0, or smart manufacturing. The award will allow the center to increase efforts to improve the skills of the next generation of engineers and the existing workforce to take full advantage of those technologies in their operations.
“With this award, we are building upon our original mission and expanding our research and services in key areas,” said Gregory Harris, ICAMS director and associate professor in the Samuel Ginn College of Engineering's Department of Industrial and Systems Engineering.
Gregory Purdy, assistant professor of industrial and systems engineering, is a co-principal investigator on the award and an ICAMS collaborating faculty member. He explained that one new focus of the funding will be devoted to the creation of the nation’s first cyber-physical manufacturing range (CpMR) housed on a university campus. The CpMR will provide a testbed to research, test, demonstrate and teach the technologies and processes to significantly improve technology adoption in small and medium-sized manufacturers and overcome the fear of malicious cyber activity in their systems.
“Industry 4.0 driven manufacturing environments are a collection of different equipment and technologies that increase the potential attack surface for malicious cyberattacks,” Purdy explained. “We are trying to understand what vulnerabilities exist in these systems and the potential impacts of a cyberattack on both the process and resulting part. However, it is not feasible to simulate attacks on a production resource that is used day-in and day-out.”
The CpMR solves this dilemma by incorporating modern manufacturing technologies in an Industry 4.0 ecosystem with current generation automation, thereby allowing a safe environment for testing and evaluating malicious cyber activity in an Industry 4.0 smart manufacturing platform.
“It allows students, researchers and other professionals to execute attacks and see what the outcome is in a state-of-the-art machining cell,” Purdy said. “I could unleash the most potent and sophisticated attack that I have and completely make everything go haywire, without endangering a key production resource.”
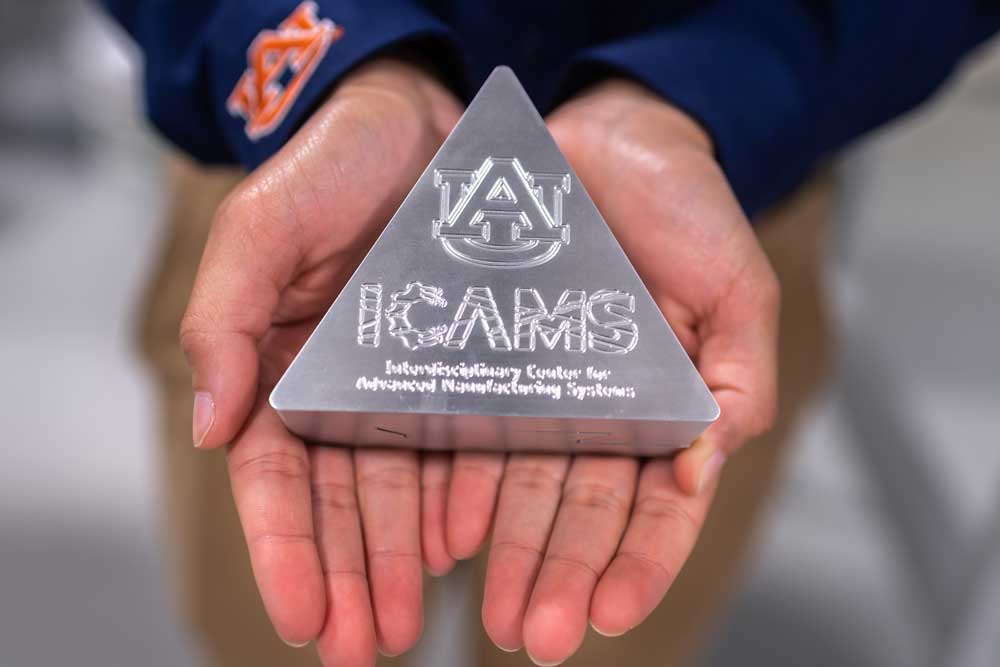
The new funding will also support the purchase of additional manufacturing equipment to further develop an Industry 4.0 manufacturing environment, including the creation of a digital manufacturing demonstration cell. The manufacturing and metrology cell will demonstrate the full digital manufacturing process flow starting by automatically scanning a subject and creating a point cloud from the 3D scan that is converted into a solid model. This model will be sent to a vertical machining center that will produce the part. A robotic arm will remove the part from the mill and deliver it to a coordinate measurement machine. The automated inspection process will then confirm the part matches the reference design. The digital manufacturing demonstration cell will be able to continuously run a product and show the capability of the connected enterprise.
“This additional equipment is going to make us more capable and allow us the ability to better showcase digital manufacturing demonstrations on site,” Harris explained. “We can show that this artifact can go all the way from design through production with little to no human intervention, really highlighting digital manufacturing capabilities. Manufacturers will be able to relate to that and say, ‘if they can do that with this artifact, I can envision what I’m trying to do using this technology.’”
According to Harris, another of those key areas of service is a “Path to the Plains” partnership with Southern Union State Community College (SU), where SU students can take Auburn University courses while completing their associate degree. The partnership also outlines a plan for a graduate certificate in advanced manufacturing and an advanced manufacturing minor. Additionally, any Auburn undergraduate student will be able to obtain a certificate in mechatronics through the partnership with SU. Participating students will be assisted by scholarships to support their educational success.
“The ability at ICAMS to create tailored programs upon request from industry allows local industries to adapt to changing industry trends much more easily using existing personnel,” said Lewis Payton, ICAMS associate director and professor of practice in the Department of Industrial and Systems Engineering. “Auburn students in the new manufacturing minor will also be graduating with hands-on experience using industrial grade equipment. ICAMS is poised to become the premier fabrication and teaching laboratory in the Southeast, including future expansion into the area of die fabrication and repair.”
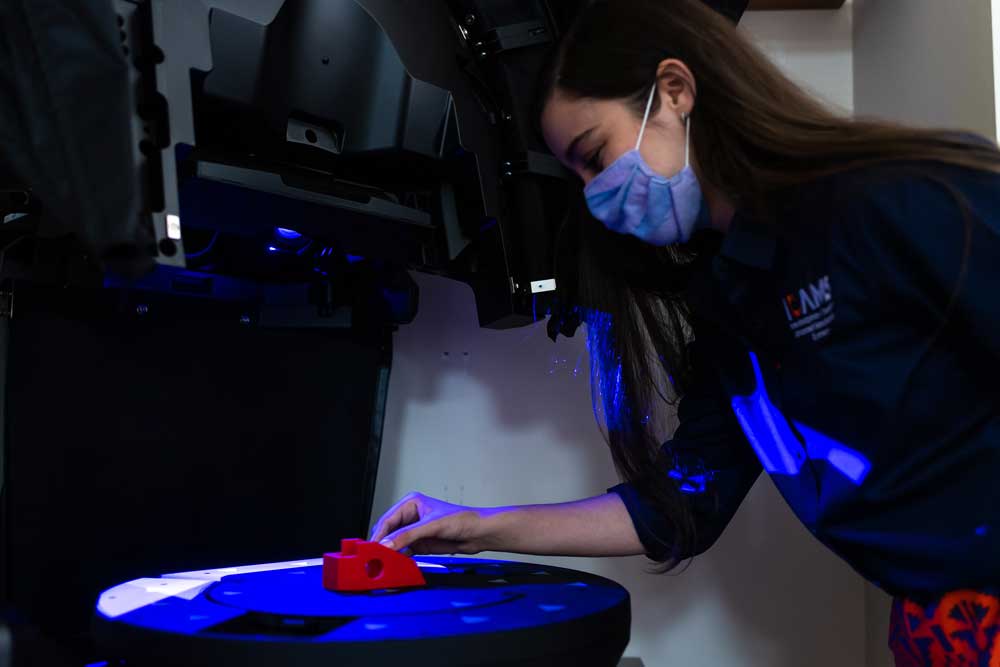
Other ICAMS services that will be introduced or enhanced with this recent award include:
- An annual call for undergraduate and graduate research proposals to be evaluated and awarded to those that expand the demonstration, education training and research capabilities of ICAMS.
- Research into inspection technologies to understand how to provide real-time quality data as feedback to adjust equipment controls to continuously improve control limits and reduce the possibility of a defective product.
- The creation of a smart cyber-physical sensing, modeling and control digital twin infrastructure with augmented and mixed reality.
- The extension of annual survey research for three additional years, for a total of a five-year study into technology adoption amid small and medium-sized manufacturers.
“ICAMS represents a major, transformational change in the areas of outreach, innovation and education at Auburn University,” Payton said. “By early in 2022, ICAMS will be the most capable prototyping laboratory within the state of Alabama for innovation, creating a unique opportunity for companies and for student design teams across the campus.”
Adele Ratcliff, director of the DoD IBAS program which is funding the effort, commended the ICAMS project’s goal of reducing the barriers against Industry 4.0 technologies being implemented in small and medium manufacturing company operations.
“The ICAMS comprehensive approach of providing technical support, project planning, skilled workers and a way to test new technology’s real-life impact on production flows is a forward-leaning model that has been proven to overcome technology-adoption hesitancy in companies of all sizes,” Ratcliff said. “Larger manufacturers have the resources to fund these risk reduction activities on their own. By partnering with small and medium manufacturers, ICAMS allows these companies to have confidence that their technology implementation projects will provide valuable process and capability improvements with limited operational risk.”
ICAMS, which launched in 2018, has formed and strengthened relationships with the city of Auburn Industrial Development Board and the Alabama Community College System. Through these relationships, ICAMS has doubled its facility footprint from 10,000 square-feet to 20,000 square-feet, providing adequate space for its dedicated operations, and utilized the space to educate and train students and industry personnel to use the advanced manufacturing technologies and capabilities to benefit the DoD and its supporting manufacturing sector.
Media Contact: , cmontgomery@auburn.edu, 334.844.3668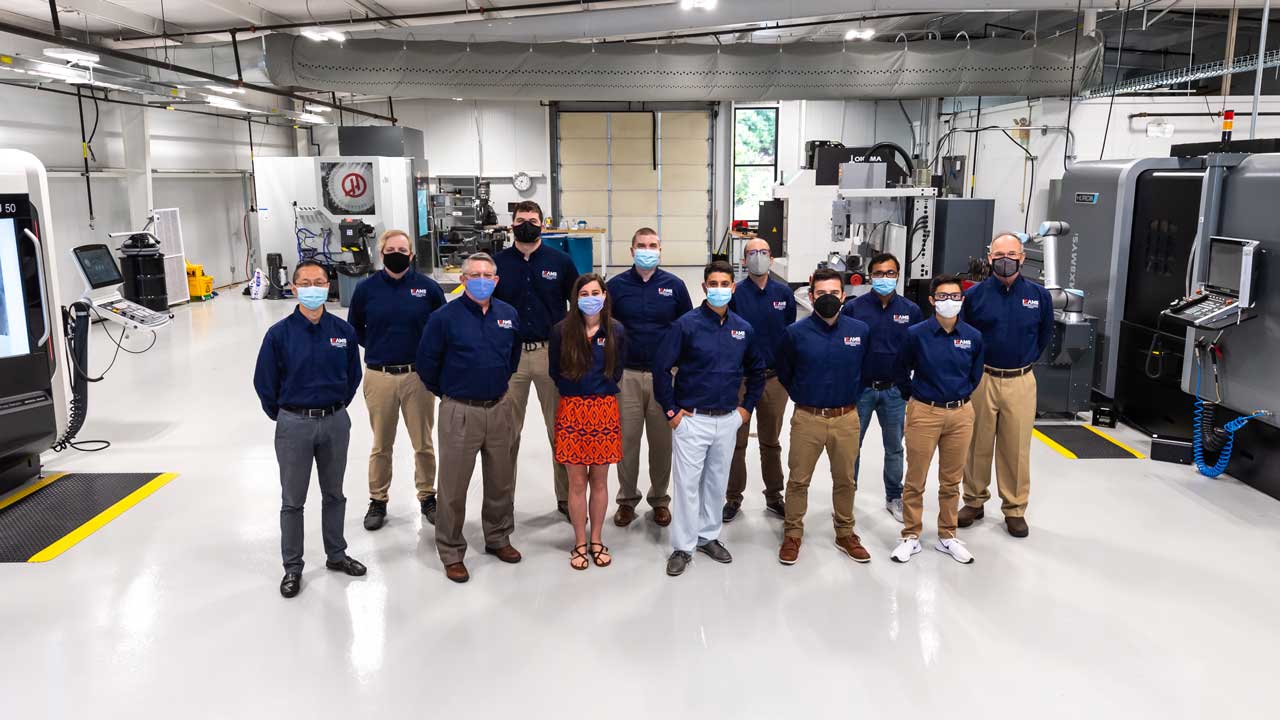
ICAMS collaborating faculty members and graduate students.